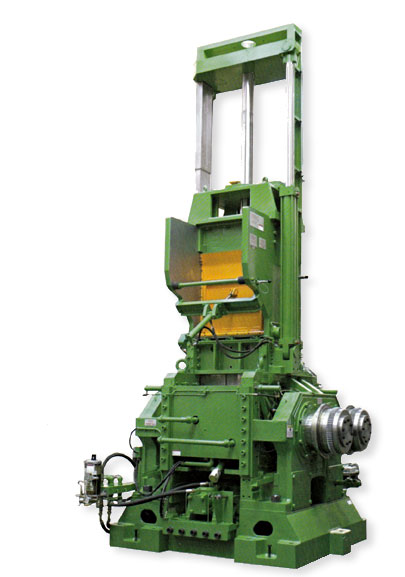
Принципиальным узлом, определяющим тип резиносмесителя, его производительность, и технологические процессы цикла смешения, являются ротора резиносмесителя. Именно их конструктивное отличие и проводит грань между смесителями тангенциального типа, и смесителями мероторного действия. Поэтому представляется логичным при обзорном рассмотрении резиносмесителя того, или иного типа, начать это рассмотрение с конструктивных особенностей роторов.
Ротора тангенциального смесителя.
Конструкция роторов достаточно долго вынуждала технологов искать компромисс между такими характеристиками, как вмешиваемость ингредиентов (диспергирование) и распределение смеси в цикле смешения. Эти два параметра находятся в конфликте в тангенциальном смесителе, что определяется самим принципом тангенциального смешения, при котором напряжение сдвига, являющееся необходимым условием диспергирования материалов, испытывает довольно малая часть ингредиентов, находящихся в камере. А именно, только та часть, которая находится у кромки лопасти ротора в момент достижения рабочего зазора со стенкой полукамеры. Но максимальная ширина лопасти на самых больших смесителях не превышает 3х – 4х сантиметров. Это вынуждало технологов искать компромисс, и выбирать угол расположения лопастей обоих роторов, решая увеличивать ли дисперсию, снижая распределение материала, или наоборот, увеличить распределение за счет снижения дисперсии.